Works Orders Demystified: Understanding Their Significance
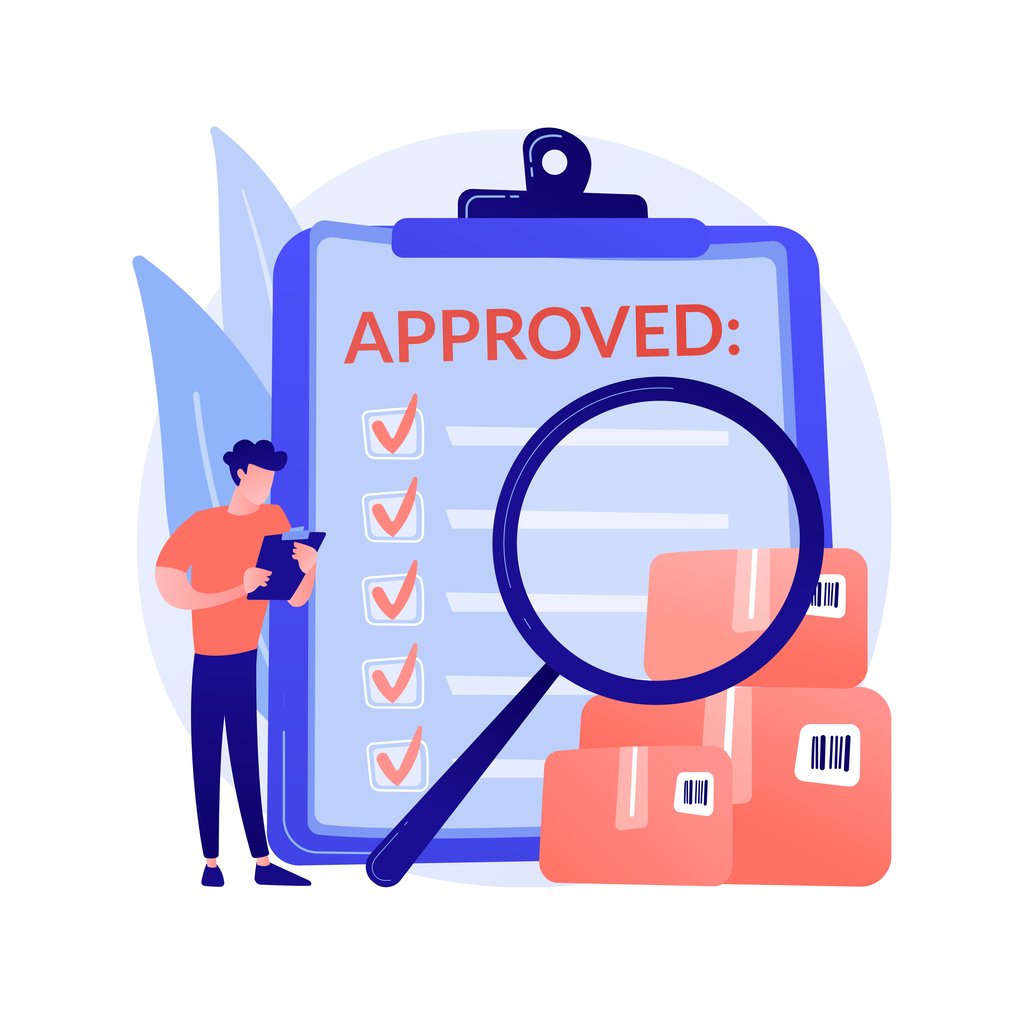
Whether you’re running a small start up or managing a large-scale corporation, understanding work orders is crucial to streamlining your procurement process. In this blog post, we will look into the world of work orders, exploring their purpose, different types, creation and management, best practices for utilization, common challenges faced, and ultimately, how they play an indispensable role in boosting your business’s success.
The Purpose of Work Orders
Work orders serve as a crucial tool for businesses to effectively manage their operations. These documents outline the specific tasks that need to be completed, ensuring that work is carried out efficiently and in a timely manner. But what exactly is the purpose of work orders?
Work orders provide clarity and direction. They clearly define the scope of work, outlining what needs to be done, who is responsible for completing it, and any deadlines or milestones that need to be met. This helps eliminate confusion and ensures everyone involved understands their role and responsibilities.
Work orders help with resource allocation. By detailing the necessary materials, equipment, or personnel required for each task or project, businesses can ensure they have everything they need before starting the job. This prevents delays caused by missing resources and enables better planning.
Work orders play a vital role in tracking progress and measuring performance. As each task is completed within a work order, it can be marked off or updated accordingly. This allows managers to monitor how much has been accomplished versus what still needs to be done.
Moreover, work orders facilitate communication between different departments or teams within an organization. They act as a central reference point where information about ongoing projects can easily be accessed by all relevant parties. This promotes collaboration, discussion, and coordination among team members, resulting in smoother workflow.
Different Types of Work Orders
Work orders come in various forms depending on the specific tasks and processes involved. Understanding the different types of work orders is essential for effective management and organization within a business.
1. Maintenance Work Orders: These work orders are commonly used in facilities management to handle repairs, inspections, or preventive maintenance tasks. They ensure that equipment, machinery, and infrastructure are properly maintained to avoid breakdowns or disruptions.
2. Production Work Orders: These work orders are prevalent in manufacturing environments where products are assembled or produced. They outline the necessary steps, materials, and resources required to complete each production run efficiently.
3. Service Work Orders: Service-based industries often rely on these work orders to schedule and track customer requests for repairs, installations, or other services. They help service providers allocate resources effectively and ensure timely completion of tasks.
4. Purchase/Procurement Work Orders: Purchase/Procurement work orders pertain to acquiring goods or services from external suppliers. They detail specifications, quantities needed, delivery dates, pricing agreements and terms negotiated with vendors.
5. Project Work Orders: For businesses engaged in project-based work such as construction or software development companies use project work orders to define scope of work deliverables timelines milestones responsibilities etc ensuring smooth execution
Understanding the different types of work orders allows businesses to tailor their processes accordingly for optimal efficiency and productivity levels across various departments.
How Work Orders are Created and Managed
Work orders play a crucial role in the smooth functioning of any business operation. They serve as the backbone for organizing and managing tasks, ensuring that everything runs seamlessly. But how exactly are work orders created and managed? Let’s dive into this process.
Creating a work order typically begins with identifying the need for a task or project. This could be triggered by various factors such as maintenance requirements, customer requests, or production demands. Once the need is identified, it is important to gather all relevant information related to the task at hand.
The next step involves creating a detailed description of the work order, including specifics like what needs to be done, who will perform it, when it should be completed by, and any additional resources required. This information helps ensure that everyone involved understands their responsibilities and deadlines.
After creating the work order itself, it needs to be assigned and communicated to the appropriate team members or departments responsible for its execution. Clear communication is essential here to avoid confusion or misunderstandings.
Once assigned, work orders are typically tracked using software systems specifically designed for this purpose. These systems allow managers to monitor progress in real-time and make adjustments if necessary. They also enable employees to update their status on tasks and provide feedback on any issues they encounter during execution.
Effective management of work orders involves regular monitoring and follow-up throughout their lifecycle. Managers must stay proactive in overseeing progress while addressing any roadblocks that may arise along the way.
Best Practices for Using Work Orders
When it comes to managing work orders effectively, there are some best practices that can help streamline the process and ensure smooth operations. Here are a few tips to consider:
1. Clearly define the scope: Before creating a work order, it’s essential to clearly define the scope of work. This includes specifying the tasks to be performed, expected outcomes, and any relevant deadlines or milestones.
2. Assign responsibility: Assigning responsibility is crucial for ensuring accountability and avoiding confusion. Clearly identify who will be responsible for executing each task outlined in the work order.
3. Provide detailed instructions: To avoid any misunderstandings or errors, provide detailed instructions within the work order itself. Include step-by-step guidelines, reference materials if necessary, and any specific requirements or preferences from stakeholders.
4. Set realistic timelines: When setting timelines for completion of tasks, it’s important to be realistic and consider factors like available resources and dependencies on other tasks or departments.
5. Track progress regularly: Regularly tracking progress against work orders helps identify bottlenecks early on and allows for timely adjustments if needed. Utilize project management tools or software that enable real-time updates and collaboration among team members.
6. Communicate effectively: Effective communication is key throughout the entire process of using work orders – from creation to execution and closure. Ensure all relevant parties are informed about changes or updates related to their respective tasks.
By following these best practices when using work orders in your business operations, you can enhance efficiency, promote transparency, reduce errors, and ultimately achieve better results.
Common Challenges with Work Orders and How to Overcome Them
1. Lack of Clarity: One common challenge with work orders is that they may lack clear instructions or details, leading to confusion among employees. To overcome this, it’s crucial to provide detailed and precise information in the work order. Include specific tasks, deadlines, and any necessary supporting documents or references.
2. Poor Communication: Miscommunication can hinder the effective execution of work orders. To address this challenge, establish a streamlined communication channel between supervisors, team members, and stakeholders involved in the work order process. Regularly update everyone on progress, changes, or any issues that arise.
3. Inefficient Workflow: Another challenge is an inefficient workflow caused by delays or bottlenecks in the work order system. Implementing a digital platform for creating and managing work orders can greatly improve efficiency by automating processes such as assigning tasks and tracking progress.
4. Resource Allocation: Allocating resources effectively is essential for successful completion of work orders. The challenge lies in ensuring that resources are available when needed without causing conflicts or shortages elsewhere. Proper planning and coordination are key to overcoming this challenge.
5. Maintenance Planning: For businesses involving maintenance projects like equipment repairs or facility upkeep, scheduling preventive maintenance efficiently can be challenging.
To overcome this issue, it’s important to have a comprehensive maintenance plan. Use historical data, to determine optimal schedules, and prioritize critical assets based on their importance.
Leveraging technology solutions like Computerized Maintenance Management Systems(CMMS)can help streamline scheduling, maintain records, and ensure timely completion of maintenance tasks.
6. Unforeseen Changes: Work orders may need adjustments due to unexpected circumstances such as equipment breakdowns, supply chain disruptions or changes in project scope. It’s important to be flexible and adapt quickly. Incorporate regular check-ins and feedback loops during the execution phase.
Importance of Utilizing Work Orders in Business Operations
Efficient business operations are crucial for any organization’s success. One key element in streamlining these operations is the utilization of work orders. These documents serve as a roadmap, guiding employees through various tasks and ensuring that everything runs smoothly.
Work orders play a vital role in managing resources effectively. By clearly outlining the required materials, equipment, and labor needed for each task, work orders help prevent delays and reduce wastage. This ensures that projects stay on schedule and within budget.
Moreover, utilizing work orders improves communication between different departments or teams involved in a project. With detailed instructions provided in the document, there is less room for misinterpretation or confusion. This leads to better collaboration and coordination among team members.
Another significant benefit of utilizing work orders is their ability to enhance accountability within an organization. Each task assigned within a work order can be tracked from start to finish, allowing managers to monitor progress closely. If any issues arise during the process, they can be addressed promptly to minimize disruptions.
Furthermore, accurate record-keeping becomes easier with the use of work orders. These documents provide valuable information about completed tasks, associated costs, and timeframes for future reference or analysis purposes.
Conclusion
In this article, we have demystified work orders and uncovered their significance in business operations. We explored the purpose of work orders, the different types available, and how they are created and managed. We also discussed best practices for using work orders and addressed common challenges that may arise.
Work orders play a vital role in procurement processes by ensuring efficient workflow management, facilitating communication between departments, and tracking progress on tasks or projects. By using work orders effectively, businesses can streamline their operations, enhance productivity, improve customer satisfaction, and ultimately drive success.
It is important to remember that each organization’s needs may vary when it comes to work order management. Therefore, adopting customizable software solutions or utilizing professional services can greatly benefit companies seeking to optimize their procurement processes.
By understanding the significance of work orders and implementing them strategically within your business operations, you can create a more organized and efficient working environment. Embrace the power of work orders today to unlock enhanced productivity and achieve your business goals.