What is Bill Of Materials (Bom)? Definition
A bill of materials is a comprehensive list of items that are required to build, manufacture, or assemble a product or service. The bom includes raw materials, components, sub-assemblies, and finished products. It also includes the quantity of each item, the unit price, and the total cost. A bom can be created for any type of product or service. A bill of materials is also sometimes referred to as a product structure tree or an ingredient list.
What is a Bill of Materials (BOM)?
A bill of materials or product structure is a list of the raw materials, sub-assemblies, intermediate assemblies, sub-components, parts, and the quantities of each needed to manufacture an end product. Bills of material are often used in engineering and manufacturing settings as a way to provide visibility into the production process.
Bills of materials can be broken down into different levels. The first level would be a top-level assembly that contains all the sub-assemblies and components needed to create the final product. Each subsequent level would contain more detailed information about the lower-level assemblies and components until you get to the individual part level.
At the heart of every BOM is a master list of all the unique parts that go into making a product. This master list is typically maintained by engineering and includes things like:
Part name
Part number
Description
Drawing or picture (CAD file)
Material specs
Tolerances
And any other critical information needed to identify and procure the part
Parts on the master list will have a unique identifier (ID), which can be used to track where it’s used in an assembly. When creating a BOM for an assembly, you’ll start with this master list and then add in additional columns to specify things like:
The quantity of each part needed for one unit of your final product
Which specific revision or version of that part you need
Where that part is sourced from
The different types of BOMs
There are three different types of bill of materials: Manufacturing BOM, Engineering BOM, and Sales BOM.
1. Manufacturing BOM: This type of bill of materials lists all the raw materials, component parts, and finished products that are required to manufacture a product. It includes information such as item number, description, quantity, unit of measure, and price.
2. Engineering BOM: This type of bill of materials contains all the information that is necessary for an engineer to understand the design and function of a product. It includes information such as component numbers and descriptions, engineering drawings, and manufacturing specifications.
3. Sales BOM: This type of bill of materials is used by salespeople to generate quotes for customers. It includes information such as item number, description, quantity, unit of measure, and price.
The benefits of using a BOM
A Bill of Materials or product structure (BOM) describes the assemblies, components, and materials needed to create a product. It provides detailed information about the parts that make up a product, including the name, description, quantity, and unit price of each component.
The benefits of using a BOM include:
1. Better visibility into the cost of goods sold (COGS).
2. Improved accuracy for inventory valuation.
3. More accurate tracking of inventory levels.
4. The ability to quickly generate assembly instructions.
5. greater insight into the manufacturing process.
How to create a BOM
A BOM is a list of all the materials, components, parts and assemblies required to build, repair or maintain a product or service. The BOM includes all the information necessary to procure or manufacture the product or service.
Creating a BOM can be a simple as listing all the materials needed to build a widget in a spreadsheet. More complex products may require a hierarchical BOM that shows the relationship between assemblies, subassemblies and components.
There are several software applications that can be used to create and manage BOMs. Some of these applications are designed specifically for managing engineering data and supporting manufacturing operations. Others are more general purpose project management or product lifecycle management applications that have features for managing BOMs.
Once you have decided which application to use, you will need to populate the application with data about the materials, components and assemblies required to build your product. This data can come from a variety of sources, including engineering drawings, CAD models, supplier catalogs and previous BOMs.
BOM software
BOM software is a type of software that helps businesses manage their bill of materials. This software can help businesses keep track of their inventory, create and manage bills of materials, and track production costs. This type of software can also help businesses plan and manage production schedules.
Conclusion
A bill of materials is a complete list of the components and materials needed to build a product. It’s an important tool for manufacturers, as it ensures that all the necessary parts are available and accounted for. A bill of materials can also be used to estimate the cost of manufacturing a product. If you’re planning on starting your own business, it’s essential that you understand what a bill of materials is and how to create one.
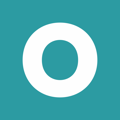
Dedicated to bringing readers the latest trends, insights, and best practices in procurement and supply chain management. As a collective of industry professionals and enthusiasts, we aim to empower organizations with actionable strategies, innovative tools, and thought leadership that drive value and efficiency. Stay tuned for up-to-date content designed to simplify procurement and keep you ahead of the curve.