Maximizing Efficiency: How Economic Order Quantity can Streamline Your Procurement Process
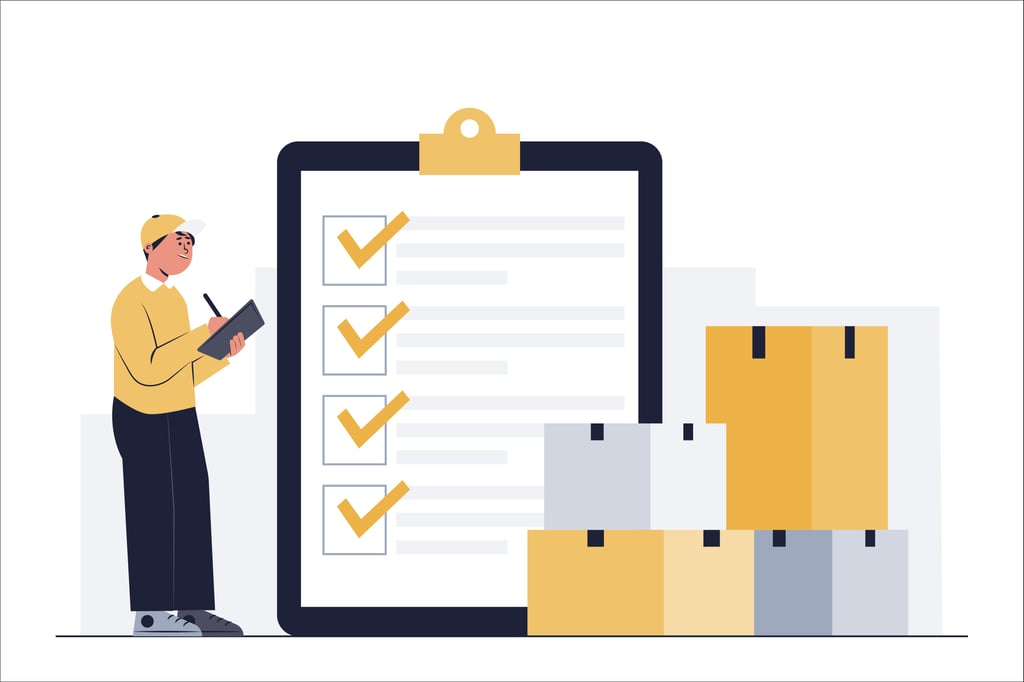
Introduction to Economic Order Quantity
Are you tired of constantly managing your inventory and procurement process? Do you find it difficult to strike a balance between overstocking and stockouts? Look no further than Economic Order Quantity (EOQ)! EOQ is a proven method for streamlining your procurement process, minimizing waste, and maximizing efficiency. In this blog post, we’ll discuss what EOQ is, how it’s calculated, the benefits of using it in your business operations, and how to successfully implement it into your procurement process. With the help of EOQ, you can take control of your inventory management system and improve overall profitability.
How EOQ is Calculated
Calculating the Economic Order Quantity (EOQ) can be done by using a simple formula that takes into consideration various factors to determine the optimal amount of inventory to order. The EOQ formula considers the annual demand for an item, the cost of ordering and holding inventory, and the lead time it takes to receive an order.
To calculate EOQ accurately, one must first know their average annual demand for each product. This information helps in determining how frequently one needs to place orders. A company’s procurement team should also consider its carrying costs like storage fees, insurance premiums and opportunity costs when deciding on how much stock they want to hold at any given point.
The next step is figuring out what it costs you every time you place an order – this includes things like shipping fees or processing charges. Once these variables are determined, they can all be used together with lead times which estimate how long it will take from placing your order until receiving delivery of goods ordered.
By calculating these details carefully with precision based on reliable data sources and making use of EOQ formulas available online or through software programs designed specifically for tracking inventory levels efficiently companies gain insights which help them make informed decisions about their procurement process while minimizing waste.
The Benefits of Using EOQ
Implementing Economic Order Quantity (EOQ) into your procurement process can bring various benefits to your business. One of the main advantages is reducing inventory costs by optimizing order quantities and minimizing excess stock. EOQ also allows for better cash flow management, as you’ll be ordering goods only when necessary, decreasing the amount of money tied up in inventory.
Using EOQ can help you avoid stockouts by ensuring that you always have enough inventory on hand to meet customer demand without overstocking. This means fewer missed sales opportunities and improved customer satisfaction levels. By streamlining procurement processes using EOQ calculations, companies can also improve their supply chain efficiency, reduce lead times and minimize transportation expenses.
Another benefit of using EOQ is increased accuracy in forecasting future demand and planning production schedules accordingly. Accurate forecasting helps businesses plan for seasonal variations or unexpected fluctuations more effectively so they can meet customer demands while avoiding unnecessary waste or shortages.
Incorporating EOQ into your procurement process brings multiple advantages that can help organizations optimize operations while managing costs more efficiently.
Implementing EOQ into Your Procurement Process
Now that you have a better understanding of EOQ and its benefits, it’s time to implement it into your procurement process. Here are some steps you can take to get started:
1. Gather data: To calculate EOQ accurately, you will need data on demand for the product, ordering costs, and holding costs.
2. Calculate EOQ: Once you have the necessary data, use the EOQ formula (mentioned in the previous section) to determine the optimal order quantity.
3. Determine safety stock levels: Safety stock is extra inventory kept on hand to account for unexpected increases in demand or delays in delivery times. You’ll want to factor this into your calculations when determining order quantities.
4. Monitor inventory levels: Keep track of your inventory levels regularly and reorder when necessary based on your calculated EOQ.
5. Evaluate results: After implementing EOQ into your procurement process, evaluate its effectiveness regularly by analyzing cost savings and comparing actual inventory levels with predicted levels.
By following these steps and continually monitoring and evaluating results, you can streamline your procurement process while minimizing costs associated with excess inventory or missed sales opportunities due to insufficient stock levels.
Conclusion
In summary, implementing Economic Order Quantity (EOQ) into your procurement process can help streamline inventory management and increase efficiency. By calculating the optimal order quantity based on demand and holding costs, you can reduce excess inventory and avoid stockouts.
With EOQ, you can also save time and money by reducing the number of orders placed and minimizing storage costs. Additionally, it provides a data-driven approach to making informed decisions about ordering and restocking.
While there may be some initial setup required to implement EOQ into your procurement process, the benefits in terms of increased productivity and cost savings are well worth it.
Incorporating EOQ into your overall supply chain strategy is an effective way to optimize inventory levels while maximizing profitability. It’s definitely something every business owner should consider when looking for ways to improve their procurement processes.