Cost-Plus Supply Chain: Factors for Success
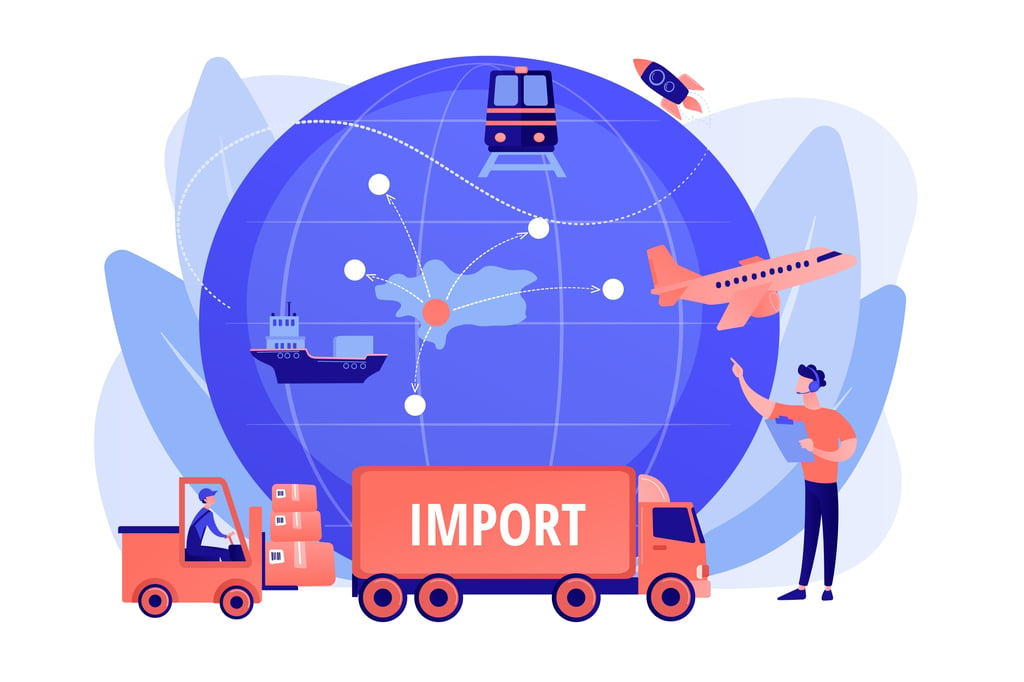
Unlocking the secrets to a successful supply chain is like discovering hidden treasure for businesses. With so many models and strategies available, it can be overwhelming to choose the right one that aligns with your company’s goals and objectives. One such model that has gained traction in recent years is the cost-plus supply chain. This innovative approach not only focuses on managing costs effectively but also ensures transparency and collaboration with suppliers.
Understanding the Cost-Plus Supply Chain Model
The cost-plus supply chain model is a procurement strategy that focuses on transparency, collaboration, and cost management. Unlike traditional supply chains where prices are negotiated independently with suppliers, the cost-plus model takes a different approach.
In this model, costs incurred by suppliers are transparently shared with buyers. The supplier‘s profit margin is then added to these costs to determine the final price of goods or services. This ensures fairness and eliminates hidden markups.
By implementing a cost-plus supply chain, businesses gain greater visibility into supplier costs and can make informed decisions based on actual expenses. This enables more accurate pricing strategies and budgeting processes.
Furthermore, the cost-plus model encourages collaboration between buyers and suppliers. By sharing information openly, both parties can work together to identify areas for improvement and implement cost-saving measures effectively.
Understanding the intricacies of the cost-plus supply chain model is essential for businesses looking to optimize their procurement practices while fostering stronger relationships with their suppliers. It provides a foundation for fair pricing negotiations, greater transparency throughout the supply chain process, and opportunities for strategic collaborations that benefit all stakeholders involved.
Benefits of Implementing a Cost-Plus Supply Chain
The benefits of implementing a cost-plus supply chain model can be significant for businesses in various industries. One key advantage is the transparency it offers in terms of pricing and costs. With this approach, companies have a clear understanding of how much they are paying for each component or service within their supply chain.
Another benefit is the ability to better manage and control costs. By having detailed visibility into the expenses associated with procurement, companies can make more informed decisions about pricing strategies, budgeting, and resource allocation.
Additionally, implementing a cost-plus supply chain model can foster stronger relationships with suppliers. When both parties have a clear understanding of costs and margins, it becomes easier to negotiate fair agreements that benefit everyone involved.
Furthermore, this approach provides greater flexibility when it comes to managing unexpected changes or disruptions in the supply chain. By having access to accurate cost data, companies can quickly adjust their pricing models or find alternative suppliers if needed.
Adopting a cost-plus supply chain model enables businesses to gain better control over their procurement processes while fostering transparency and trust throughout their supplier network. It’s an effective strategy for optimizing costs and improving overall operational efficiency.
Key Factors for Success in the Cost-Plus Supply Chain Model
To ensure success when implementing a cost-plus supply chain model, there are several key factors that businesses need to consider. Let’s explore these factors in more detail.
1. Strong Supplier Relationships: Building and maintaining strong relationships with suppliers is crucial in the cost-plus supply chain model. By establishing trust and open communication, businesses can negotiate favorable pricing terms and secure reliable sources of goods or services.
2. Accurate Cost Analysis: Conducting thorough cost analysis is essential to determine accurate product costs. This involves evaluating direct material costs, labor expenses, overheads, transportation fees, and any other relevant expenditures. With precise cost information, businesses can set appropriate prices that cover all expenses while ensuring profitability.
3. Effective Demand Forecasting: Having an accurate demand forecast allows businesses to plan their procurement activities effectively. By understanding customer demands and market trends, companies can optimize inventory levels and avoid overstocking or understocking situations.
4. Efficient Inventory Management: Implementing efficient inventory management practices helps reduce carrying costs associated with excess stock while avoiding stockouts that may disrupt operations or lead to lost sales opportunities.
5. Robust Data Analytics: Leveraging data analytics tools enables businesses to gain valuable insights into their supply chain performance metrics such as lead times, order accuracy rates, on-time deliveries, etc. These insights help identify areas for improvement and make data-driven decisions in managing procurement processes.
6. Supplier Performance Evaluation: Regularly assessing supplier performance ensures that they meet quality standards consistently while delivering products or services on time at competitive prices.
By focusing on these key factors for success in the cost-plus supply chain model, businesses can streamline their procurement process efficiently while maintaining competitive pricing strategies without compromising profitability.
Effective Strategies for Managing Costs and Suppliers
In today’s competitive business landscape, managing costs and suppliers is crucial for the success of any organization. Implementing effective strategies can help businesses optimize their procurement process, reduce expenses, and establish strong relationships with suppliers.
One strategy is to conduct a thorough analysis of current costs and identify areas where savings can be made. This may involve renegotiating contracts with existing suppliers or seeking alternative vendors who offer more competitive pricing. Regularly reviewing supplier performance metrics can also ensure that you are getting the best value for your money.
Another key strategy is to establish clear communication channels with suppliers. By maintaining open lines of communication, businesses can build trust and address any issues or concerns promptly. This enables both parties to work collaboratively towards achieving cost-effective solutions.
Furthermore, implementing technology-driven solutions such as automated procurement systems or e-sourcing platforms can streamline processes and improve efficiency when managing costs and suppliers. These tools allow businesses to track spending, analyze data in real-time, monitor supplier performance, and make informed decisions based on accurate information.
Additionally, developing long-term partnerships with reliable suppliers who share similar goals can lead to cost savings through bulk purchasing discounts or improved terms. Building strong relationships based on mutual trust allows for better collaboration in problem-solving and ensures a steady supply chain.
Regularly evaluating the effectiveness of implemented strategies is essential in managing costs and improving supplier relations over time. Conducting periodic audits helps identify areas that need improvement while recognizing successful practices that should be continued.
By implementing these effective strategies for managing costs and suppliers within your organization’s procurement process, you will not only optimize your supply chain but also enhance overall profitability.
Potential Challenges and How to Overcome Them
Potential Challenges and How to Overcome Them:
1. Supplier ReliabilitySupplier Reliability challenges in implementing a cost-plus supply chain is ensuring that suppliers deliver materials and products on time consistently. Delays or disruptions can lead to increased costs, missed deadlines, and dissatisfied customers. To overcome this challenge, it is crucial to establish strong relationships with reliable suppliers who have a track record of timely deliveries. Regular communication, performance monitoring, and contingency plans can also help mitigate risks associated with supplier unreliability.
2. Cost Fluctuations:
Another challenge in the cost-plus supply chain model is dealing with fluctuations in raw material prices or unforeseen increases in production costs. These fluctuations can impact profit margins if not properly managed. To address this challenge, businesses should closely monitor market trends and engage in proactive price negotiations with suppliers. Implementing robust cost tracking mechanisms, such as regular audits and real-time reporting systems, can provide greater visibility into cost variances and enable timely adjustments.
3. Supply Chain Complexity:
The complexity of managing multiple suppliers across different geographies or coordinating various logistical activities poses another significant challenge for organizations adopting the cost-plus model. To navigate this complexity successfully, businesses should invest in advanced technology solutions like procurement software or inventory management systems that streamline processes and enhance efficiency.
4. Market Volatility:
The unpredictability of global markets adds an additional layer of difficulty to the cost-plus supply chain model. Economic recessions or political events may disrupt demand patterns or create new trade barriers that impact sourcing strategies and logistics operations significantly.
To mitigate these risks effectively, companies need to stay informed about market changes through continuous monitoring of industry trends and establishing flexible contingency plans.
By proactively addressing these potential challenges head-on through effective supplier management practices, robust risk mitigation strategies and technological investments, businesses can maximize the benefits offered by a well-executed cost-plus supply chain.
Conclusion
After exploring the cost-plus supply chain model, its benefits, key success factors, effective strategies, and potential challenges, you may be wondering if this model is right for your business. While there is no one-size-fits-all answer to this question, considering a few crucial factors can help you make an informed decision.
Assess the nature of your business and industry. The cost-plus supply chain model tends to work best in industries where costs fluctuate frequently or are difficult to predict accurately. If your business operates in such an industry and experiences significant variability in costs or supplier pricing structures, adopting a cost-plus approach might provide more stability and control over expenses.
Evaluate your relationship with suppliers. Implementing a cost-plus supply chain requires strong relationships with reliable suppliers who are open to transparent collaboration on pricing mechanisms. If you have established long-term partnerships built on trust and mutual understanding with your suppliers, transitioning to a cost-plus model could strengthen these relationships further.
Consider whether accurate costing information is readily available within your organization. Successful implementation of the cost-plus supply chain relies heavily on accurate data about product costs throughout each stage of procurement. If you already have robust systems in place for collecting and analyzing costing information across different departments or production facilities within your company, it may be easier to adopt this model effectively.
Importantly analyze whether implementing a new supply chain model aligns with your overall strategic goals as well as financial objectives. While the cost-plus approach has numerous advantages regarding controlling costs and maintaining profitability in certain situations; it’s essential to ensure that it aligns with other aspects of your business strategy such as customer satisfaction goals or market positioning priorities.
Ultimately deciding whether the cost-plus supply chain model is right for your business requires careful consideration of these factors along with any specific circumstances unique to your organization. It may be helpful to consult with industry experts or engage in a pilot program before making a full-scale transition.