Direct Materials and Strategic Sourcing: The Winning Combination
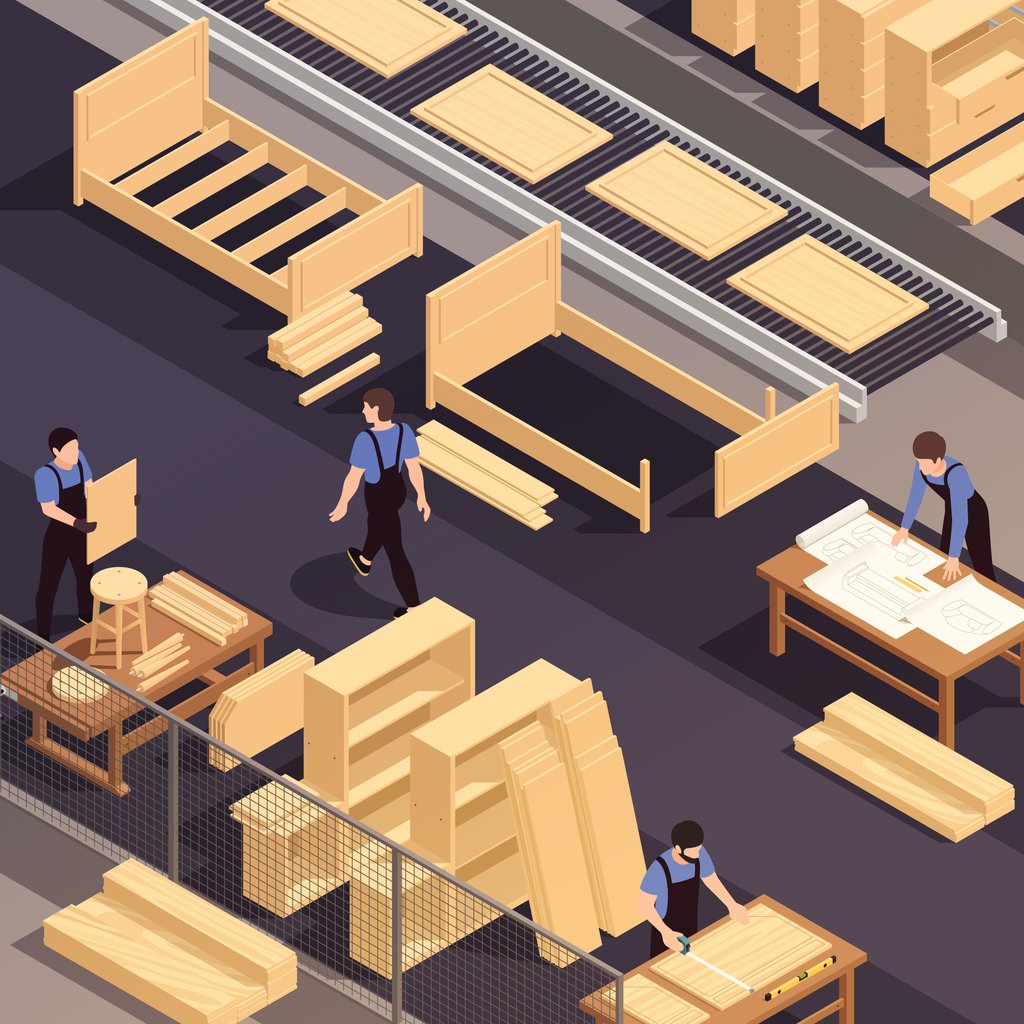
Introduction to Direct Materials and Strategic Sourcing
In the fast-paced world of manufacturing, every decision counts, especially when it comes to sourcing materials for production. Enter direct materials and strategic sourcing – a dynamic duo that can make or break a company’s success.
In this blog post, we will explore the power of combining direct materials with strategic sourcing in procurement. We’ll unravel the importance of direct materials in manufacturing and delve into the role that strategic sourcing plays in effective supply chain management.
Understanding the Importance of Direct Materials in Manufacturing
Direct materials play a crucial role in the manufacturing industry. These are the tangible resources that are transformed into finished products during the production process. From raw materials like metals and plastics to components and sub-assemblies, direct materials form the backbone of any manufacturing operation.
Without direct materials, manufacturers would not be able to produce their goods. They are essential for creating high-quality products that meet customer demands. The quality of direct materials directly impacts the overall quality of the final product, so it’s important for manufacturers to carefully select their suppliers and ensure they provide reliable and consistent materials.
Moreover, direct material costs often make up a significant portion of a manufacturer’s expenses. By effectively managing these costs through strategic sourcing practices, companies can improve their bottom line and maintain competitiveness in the market.
Strategic sourcing involves identifying, evaluating, negotiating with, and selecting suppliers who can provide high-quality direct materials at competitive prices. It requires careful analysis of supplier capabilities, cost structures, delivery timescales, and other factors that impact procurement decisions.
By strategically sourcing their direct materials, manufacturers can achieve several benefits. Firstly,
they can reduce costs by leveraging volume purchasing power or finding alternative suppliers offering more favorable pricing terms. Secondly, strategic sourcing allows manufacturers to identify potential risks within their supply chain and develop contingency plans to mitigate them. Thirdly, it helps establish long-term partnerships with reliable suppliers who understand their needs and consistently deliver high-quality materials on time.
Overall, combining strategic sourcing with effective management of direct materials is essential for successful manufacturers in today’s highly competitive global marketplace.
The Role of Strategic Sourcing in Supply Chain Management
Supply chain management plays a crucial role in the success of any manufacturing organization. It involves various processes and activities aimed at ensuring the smooth flow of goods from raw materials to finished products. One key aspect of supply chain management is strategic sourcing.
Strategic sourcing is a proactive approach to procurement that focuses on identifying, evaluating, and selecting suppliers who can provide the best value for an organization’s direct material needs. The goal is not only to find suppliers who offer competitive pricing but also those who can deliver high-quality materials consistently.
By strategically sourcing direct materials, manufacturers can gain several advantages. It allows them to build strong relationships with reliable suppliers, ensuring a steady supply of quality materials. This reduces the risk of disruptions in production and helps maintain consistent product quality.
Furthermore, strategic sourcing enables manufacturers to negotiate favorable terms with their suppliers, such as volume discounts or longer payment terms. These cost-saving measures directly impact the company’s bottom line and increase its overall profitability.
Additionally, by leveraging strategic sourcing practices, organizations can enhance their visibility into supplier performance metrics. This allows for better monitoring and evaluation of supplier reliability and responsiveness – critical factors in maintaining efficient production processes.
To implement a winning combination of direct materials and strategic sourcing effectively, there are some best practices manufacturers should follow:
1) Conduct thorough market research to identify potential suppliers.
2) Evaluate supplier capabilities based on criteria such as financial stability and technical expertise.
3) Establish clear communication channels with selected suppliers.
4) Regularly assess supplier performance through key performance indicators (KPIs).
5) Continuously monitor market trends to identify new opportunities or potential risks in the supply chain.
Benefits of Combining Direct Materials with Strategic Sourcing
When it comes to manufacturing, the combination of direct materials and strategic sourcing can yield a multitude of benefits for companies. By effectively managing and optimizing their procurement processes, manufacturers can streamline operations and drive cost savings.
One key benefit is increased efficiency. By strategically sourcing direct materials, manufacturers can ensure that they have the right quantities of raw materials at the right time, minimizing inventory costs and reducing waste. This not only improves cash flow but also enables faster production cycles, allowing companies to meet customer demands more effectively.
Another advantage is improved supplier relationships. Through strategic sourcing practices, manufacturers can identify reliable suppliers who offer competitive pricing and high-quality materials. Building strong partnerships with these suppliers allows for better collaboration and communication throughout the supply chain, leading to enhanced product quality and reduced lead times.
Moreover, combining direct materials with strategic sourcing enables risk mitigation. Manufacturers are able to diversify their supplier base, reducing dependence on a single source and minimizing vulnerability to disruptions in the market or unforeseen events. This flexibility protects against potential supply shortages or price fluctuations that could impact production schedules.
Furthermore, cost savings are a significant benefit of this winning combination. By leveraging strategic sourcing techniques such as negotiation strategies or volume discounts when procuring direct materials, manufacturers can achieve substantial cost reductions over time. These savings contribute directly to improving profitability while maintaining product quality standards.
Best Practices for Implementing a Winning Combination of Direct Materials and Strategic Sourcing
Implementing a winning combination of direct materials and strategic sourcing requires careful planning and execution. Here are some best practices to consider when integrating these two critical components:
1. Supplier evaluation: Conduct thorough research on potential suppliers, considering factors such as quality, reliability, cost-effectiveness, and sustainability. Establish clear criteria for supplier selection to ensure alignment with your organization’s goals.
2. Collaboration: Foster strong relationships with suppliers through open communication channels, regular meetings, and mutual goal-setting. Encourage transparency in sharing information to identify opportunities for improvement and innovation.
3. Risk management: Develop strategies to mitigate risks associated with supply chain disruptions or changes in market conditions. Diversify your supplier base where possible and establish contingency plans to address potential challenges.
4. Continuous improvement: Regularly assess the performance of both direct materials and strategic sourcing processes. Identify areas for improvement and implement proactive measures to enhance efficiency, reduce costs, and increase overall value.
5. Technology integration: Leverage digital tools such as e-procurement platforms or supply chain analytics software to streamline processes, improve data visibility, and facilitate real-time decision-making.
By following these best practices, manufacturers can optimize their procurement processes while maximizing the benefits of direct materials sourcing within a strategic framework.
Conclusion: Why Every Manufacturer Should Consider This Approach
When it comes to procurement and supply chain management, the combination of direct materials and strategic sourcing can be a game-changer for manufacturers. By strategically sourcing their direct materials, companies can not only optimize their costs but also enhance the overall efficiency and effectiveness of their supply chains.
Direct materials play a crucial role in manufacturing as they are the raw components needed to create finished products. Properly managing these materials is essential for ensuring smooth production processes and delivering high-quality goods to customers. Strategic sourcing, on the other hand, focuses on identifying the most cost-effective suppliers while maintaining quality standards.
By combining direct materials with strategic sourcing practices, manufacturers can achieve several benefits. They can reduce costs by negotiating favorable terms with suppliers, leveraging economies of scale, and streamlining procurement processes. This approach enables better risk management by diversifying supplier networks and ensuring continuity of supply even during unforeseen disruptions or market fluctuations.