What is Supplier Management
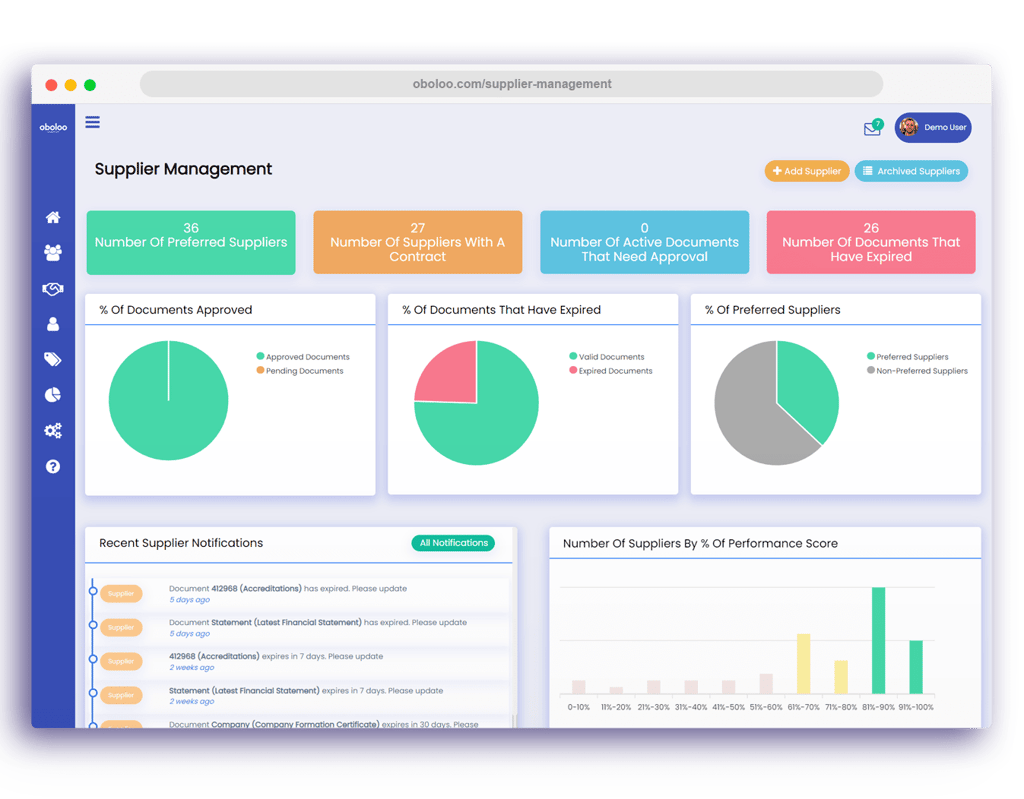
Supplier management ensures that an organization receives the best value from its suppliers. An organisation’s smooth running depends on these suppliers, so it’s important for both suppliers and organizations to work together properly.
A comprehensive supplier management policy ensures that the organization establishes a relationship with its suppliers, manages its requirements, and communicates clearly with them.
What is supplier relationship management?
An organization’s supplier relationship management (SRM) strategy involves assessing the contribution and influence of suppliers on their success, identifying tactics to improve their performance, and developing the strategy to carry these tactics forward.
What is supplier lifecycle management?
Supplier relationship management focuses primarily on post-contract management. A supplier lifecycle management (SLM) programme manages strategic and high-value suppliers throughout their entire lifecycle, from selection to end of contract. The most important part of the process is recognizing the value suppliers can provide in order to integrate those benefits into your procurement process.
What is supplier information management?
Supplier information management (SIM) involves gathering, storing, updating, and analysing all supplier data in one place. The data is in the form of financial trading information, accreditations, and certifications that are necessary to trade with the buyer.
As a result, supplier relationships are strengthened, compliance is improved, and buyer workload is reduced.
What are the steps in the supplier management process?
- Qualification – An evaluation of suppliers is required to determine if they can meet the standards set by the buyer for the provision of goods or services.
- Onboarding – Once the selected suppliers have been onboarded, the necessary information is collected. Consequently, internal processes and systems need to be modified or updated, as well as relevant stakeholders, so that the company recognizes and can begin trading with the new supplier.
- Categorisation – Categorising suppliers based on a set of predefined metrics such as supply risk, supply criticality, and total spend is the process of categorizing suppliers.
- Collaboration – A close partnership between organisations and their suppliers improves the relationship and adds value through product or service innovation and process improvements.
- Evaluation – An evaluation of a supplier’s performance is based on a number of criteria, including delivery time, price, production, quality and service, in order to ensure the contract terms are met. Arguably the most important to step to get the maximum value out of the process.
Benefits of Supplier Management
Reduced risk – Using a supplier information management system can reduce the chance of fraud between employees and suppliers, such as invoice fraud, as well as reduce supply problems in a risk-free manner.
Reduced costs – Long-term cost savings can be achieved through supplier relationship management
Increased efficiency – As the relationship develops and communication improves, suppliers gain a deeper insight into their clients’ businesses. The result is a reduction in supply chain delays and an improvement in operational efficiency.
Supplier consolidation – Buyers can streamline their purchasing process with a consolidated supply chain, making budgeting easier, streamlining the purchasing process and. enjoy economies of scale.